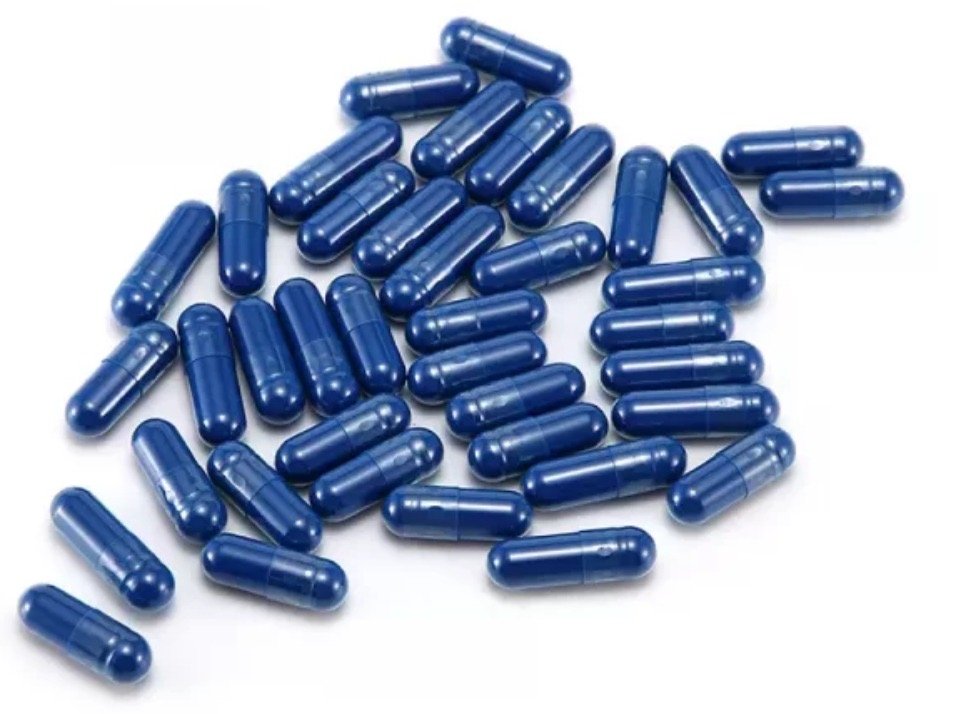
By Anna in Blogs 23/10/2023 · 6 minute capsules read
The “less is more” principle applies not just to art and architecture but also to capsule filling, especially in pharmaceuticals. Empty capsules separation challenges can be resolved by counterintuitively reducing vacuum pressure. Drawing from our experience, we’ll share five practices to cut waste and reduce machine downtime.
- Monitoring and controlling vacuum pressure at the capsule filling machine.
- Ensuring adherence to the full spectrum of OEM vacuum requirements.
- Comprehending the intricacies of empty capsules.
- Adequately setting up and inspecting machine conditions.
- Limiting the impact of fill material on processes.
- Breaking down the capsule-filling process into individual machine functions, such as rectification, separation, and filling, can refine the overall operation, ensuring it functions seamlessly.
Effective empty capsules separation is crucial and can be gauged successful when the capsules are properly seated. In the upper tool, and bodies in the lower, undamaged, as they progress toward the filling station. Failure in proper separation can manifest in various ways, such as missing caps or bodies, pinholes, and other imperfections. These issues cascade into further issues like dirty tooling, ultimately compromising productivity and yield.
Implementing a Functional Gauge and Pressure Relief Valve
The concept of “manage what you can measure” holds true in various contexts. In the realm of empty capsule filling, having a properly functioning vacuum gauge and an associated pressure relief valve is akin to ensuring clear visibility while navigating through a storm—both are essential for safeguarding operations.
These critical tools empower operators to not only set but also continuously monitor and maintain precise vacuum levels. This capability enables efficient troubleshooting and acts as a safeguard against the inadvertent application of excessive vacuum, which could potentially damage the empty capsules.
Upholding Vacuum Requirements and Navigating Capsule Expectations
It is of paramount importance to guarantee the presence of the recommended vacuum as measured at the capsule filling machine. It’s worth noting that this vacuum level may fluctuate when transitioning between different capsule filling machines, primarily due to variations in their capacity and design. Additionally, it’s crucial to acknowledge that the pre-lock force may differ among various capsule suppliers, owing to variations in pin design and manufacturing processes.
Always maintain a vigilant eye on these factors when planning and making adjustments to your capsule filling process.
Understanding Modern Empty Capsules and Handling Them Effectively
In the realm of modern encapsulation, today’s empty capsules are meticulously engineered to meet the highest standards. They boast innovative features such as pre-lock dents and strategically placed air vents. These design elements are implemented to address the exacting requirements of contemporary encapsulation techniques. With operational speeds reaching up to an impressive 400,000 capsules per hour, precision is paramount.
To safeguard the quality and functionality of these advanced capsules, it’s essential to prioritize proper storage, careful handling, and the maintenance of optimal conditions. These practices play a pivotal role in preserving the capsules’ precise dimensions and their efficient separation capabilities, ensuring consistent high-quality performance.
Ensuring Optimal Filling Machine Setup and Pristine Condition
To achieve an optimal setup for your empty capsules production process, it’s crucial to ensure a seamless transition from rectification to separation. This involves positioning the empty capsules perfectly vertical, preventing any premature closure that could hinder the separation process. To safeguard against potential issues during capsule separation, it’s essential to maintain alignment, cleanliness, and integrity of your tooling. These proactive measures will not only enhance the production flow but also minimize the risk of disruptions.
Employing Efficient Cleaning Station Practices
The evolution of tooling cleaning stations has come a long way. They’ve transitioned from being mere dust-collection hoods to incorporating advanced configurations. These configurations can now employ a blast of compressed air into tooling bores or utilize replaceable cleaning brush tips. Consequently, this transformation has resulted in a more robust and effective cleaning process. By ensuring effective cleaning practices, we can consistently maintain optimal operational conditions throughout the capsule filling process.
At FOREFRONT Nutraceuticals, our dedicated team is ever ready to assist you in navigating challenges with capsule separation or any part of the filling process. To delve deeper into capsule technology trends or for assistance with your capsule production, please don’t hesitate to connect with our team.